Job Costing and Process Costing
Introduction to Job Costing and Process Costing
Job costing and process costing are two primary methods used in cost accounting to assign costs to products or services. Understanding the differences between these methods and when to apply each is crucial for accurate financial reporting and decision-making in various industries.
Common Terms and Definitions
Cost Object: A product, service, or project for which costs are accumulated and measured.
Direct Materials: Raw materials that are directly traceable to the production of a specific product or service.
Direct Labor: Labor costs that are directly traceable to the production of a specific product or service.
Manufacturing Overhead: Indirect costs associated with the production process, such as utilities, depreciation, and indirect labor.
Cost Driver: A factor that causes a change in the cost of an activity, such as labor hours or machine hours.
Equivalent Units: A measure of the work done during a period, expressed in fully completed units.
Talk to an AI Accounting tutor.Job Costing
Job costing is a method used when a company produces unique products or services based on specific customer orders. Each job is treated as a separate cost object, and costs are accumulated for each job separately. The main characteristics of job costing include:
- Unique products or services
- Specific customer orders
- Costs are traceable to individual jobs
- Used in industries such as construction, printing, and custom manufacturing
Calculating Job Costs
To calculate the cost of a job, follow these steps:
- Identify and assign direct materials costs to the job.
- Identify and assign direct labor costs to the job.
- Allocate manufacturing overhead costs to the job using a predetermined overhead rate.
- Sum up the direct materials, direct labor, and allocated overhead costs to determine the total cost of the job.
Process Costing
Process costing is a method used when a company produces homogeneous products in a continuous process. Costs are accumulated for each process or department and then assigned to the products that pass through them. The main characteristics of process costing include:
- Homogeneous products
- Continuous production process
- Costs are accumulated by process or department
- Used in industries such as oil refining, chemical processing, and food processing
Calculating Process Costs
To calculate process costs, follow these steps:
- Determine the total costs (direct materials, direct labor, and manufacturing overhead) for each process or department.
- Calculate the equivalent units of production for each process or department.
- Compute the cost per equivalent unit for each cost category (direct materials, direct labor, and manufacturing overhead).
- Assign costs to the units completed and transferred out, and to the units remaining in work-in-process inventory.
Common Questions and Answers
What is the main difference between job costing and process costing?
Job costing is used for unique products or services based on specific customer orders, while process costing is used for homogeneous products produced in a continuous process.
When should a company use job costing instead of process costing?
A company should use job costing when it produces unique products or services based on specific customer orders, and when the costs can be easily traced to individual jobs. Examples include custom furniture manufacturers, construction companies, and print shops.
How are overhead costs allocated in job costing and process costing?
In job costing, overhead costs are allocated to individual jobs using a predetermined overhead rate based on a cost driver, such as labor hours or machine hours. In process costing, overhead costs are allocated to each process or department and then assigned to the products that pass through them.
Get your questions answered instantly by an AI Accounting tutor.Conclusion
Understanding the differences between job costing and process costing, and knowing when to apply each method, is essential for accurate cost accounting and decision-making. By mastering the concepts and calculations involved in these costing methods, you will be well-prepared to tackle real-world accounting challenges and contribute to the financial success of your organization.
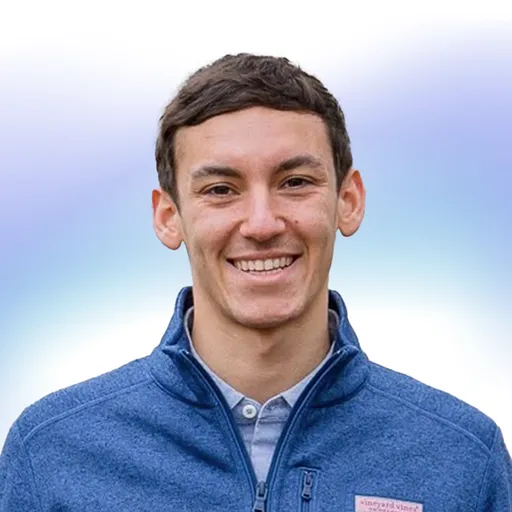
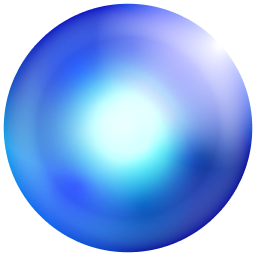