Operations Management
Introduction to Operations Management
Operations management is the administration of business practices to create the highest level of efficiency possible within an organization. It involves planning, organizing, and supervising the production of goods and services, with the goal of optimizing resources and maximizing customer value.
Common Terms and Definitions
Process: A series of activities or steps that transform inputs into outputs.
Capacity: The maximum output that a system or process can produce over a given period.
Lead Time: The time between the initiation and completion of a process, including processing, waiting, and transportation time.
Bottleneck: A point in a process where the flow of work is constrained, limiting the overall capacity of the system.
Inventory: The stock of raw materials, work-in-progress, and finished goods held by an organization.
Supply Chain: The network of organizations, people, activities, information, and resources involved in moving a product or service from supplier to customer.
Six Sigma: A data-driven approach to process improvement that aims to minimize defects and variation.
Talk to an AI Business Management tutor.Key Areas of Operations Management
Process Design: The development and implementation of efficient and effective processes for producing goods and services.
Capacity Planning: The process of determining the production capacity needed to meet changing demands for products and services.
Inventory Management: The practice of controlling and optimizing the storage and flow of raw materials, work-in-progress, and finished goods.
Quality Management: The process of ensuring that products and services meet or exceed customer expectations and industry standards.
Supply Chain Management: The coordination and integration of all activities involved in delivering a product or service, from raw materials to the end customer.
Operations Management Strategies and Tools
- Lean Manufacturing: A systematic approach to identifying and eliminating waste in production processes.
- Just-in-Time (JIT) Production: A strategy that aligns raw material orders and production with actual demand, minimizing inventory and waste.
- Total Quality Management (TQM): A comprehensive approach to quality improvement that involves all members of an organization.
- Theory of Constraints (TOC): A methodology for identifying and managing the constraints that limit a system's performance.
- Enterprise Resource Planning (ERP): An integrated software system that manages and automates key business processes across an organization.
Common Questions and Answers
What is the role of operations management in an organization?
Operations management is responsible for overseeing the production of goods and services, ensuring that resources are used efficiently and effectively to meet customer demand and achieve organizational goals.
How can operations management improve efficiency and productivity?
Operations management can improve efficiency and productivity by optimizing processes, managing capacity, reducing waste, and implementing continuous improvement initiatives such as Lean Manufacturing and Six Sigma.
What are the key challenges faced by operations managers?
Operations managers face challenges such as managing complex supply chains, balancing capacity with demand, ensuring product and service quality, and adapting to changing market conditions and customer requirements.
Get your questions answered instantly by an AI Business Management tutor.Conclusion
Operations management plays a critical role in the success of any organization by ensuring the efficient and effective production of goods and services. By understanding the key concepts, strategies, and tools of operations management, you will be well-equipped to analyze and improve business processes, optimize resource utilization, and deliver value to customers.
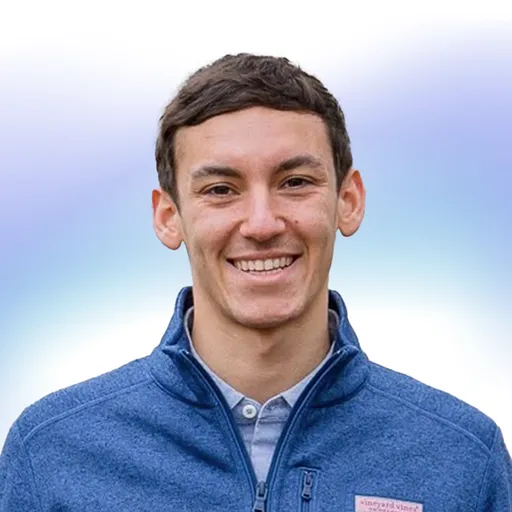
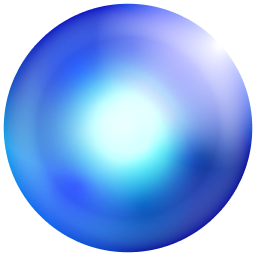